Dual CS 601 Turntable
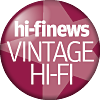
Any mention of Dual turntables usually brings one of the many incarnations of the company's CS 505 to mind. The original '505 was a typical Dual design, taking its cue from the basic turntables that had been around since the 1950s by being built on a sprung-steel plate. It was a budget deck, which sold mainly to those looking to take their first step on the audiophile ladder. But Dual made more ambitious models too.
The mainstay of its early '70s range was the 1229, a suspended-chassis, three-speed idler-drive deck that was similar in many ways to the models BSR and Garrard were making at the time, only far better engineered and much better finished. A synchronous motor and a full size (12in) platter set the 1229 apart form the herd and it sold well, despite its relatively high price of around £115 with plinth, cover and Shure DM103 cartridge.
Little Belter
Dual went further up-market in 1975 with the 701, a direct-drive, semi-automatic turntable which, it was claimed, delivered performance of a 'professional standard'. The same year it unveiled the CS 601 seen here, the first belt-drive model in its range. Supplied with a plinth, lid and factory-fitted Shure V15/III-LM cartridge [HFN Aug '73] and finished in a choice or either white or simulated walnut, the CS 601 (as the complete package was known) was not a cheap option at around £135. But 'professional' levels of performance were claimed once again.
Even though the new turntables from Japan, such as the Sony PS-X4 [HFN Sep '17], were beginning to make German company Dual's offerings look a little old fashioned, they still enjoyed a loyal following. The CS 601 featured a powerful eight-pole synchronous motor which operated almost silently and had its speed locked to the mains frequency. The arm could be operated either manually or automatically, which saw the various sequences completed in a brisk, efficient manner. The arm itself was made from an aluminium tube that was both straight and rigid and this was suspended on a self-adjusting gimbal bearing and balanced by a carefully decoupled counterweight.
As for the supplied V15/III-LM cartridge, this was the top model in the Shure range at the time and was well known for its fine tracking ability. The cost of this pick-up accounted for around £40 of the CS 601's price, showing that the turntable itself represented good value for money given the quality of what was on offer.
Home On The Range
The CS 601 remained in Dual's often bafflingly diverse and constantly changing range until around 1978, when it was replaced by models such as the CS 510 and CS 502. Both of these decks dispensed with some of the automatic functions as well as the expensive Shure cartridge and so were cheaper as a result. If one still wanted a Dual deck with a factory-fitted V15/III-LM then your choice lay between the CS 704 and 721, both of which were direct-drive.
Circular Logic
It is difficult not to be impressed by the way this deck's mechanical logic operates. It's all the more impressive when you consider that there are no electronic systems to control things, as would be the case if a similar piece of equipment were to be designed today. For example, to play a record manually all one has to do is unlock the arm from its rest and place it on the record – the motor starts automatically with no further intervention. Returning the arm to the rest switches the motor off again in the same way.
Fully automatic operation is instigated by moving the lever on the right of the plinth to 'start'. This sets the motor in motion and the arm cues in to either the 12in or 7in start point, depending on the setting of the speed control. Moving the lever to 'stop' parks the arm and stops the motor, or the manual stopping sequence can be used instead. Meanwhile, a small knob next to the control lever is used to select between single play and continuous repeat, the latter being cancelled as part of an automatic stop sequence should this be requested.
Further refinements lie beneath the surface, such as the speed change mechanism being blocked unless the platter is rotating. This prevents damage to the belt if the speed change lever is accidentally moved while the power is turned off. The controls all have a light, positive and accurate feel too, like the dashboard switches of a quality German car of the period.
Dual's unusual 'Vario Pulley' is used to give some fine speed adjustment. This clever arrangement sees the motor pulley split into eight segments whose overall diameter can be changed using a tapered pin which is pushed down into the top. With some Dual turntables this has to be done with a screwdriver, once the platter has been removed. In the case of the CS 601, however, a mechanism is provided that brings fine control of the speed out to a discrete knob, which can be found mounted in the pivot of the speed lever.
As for the platter, this rests on a larger die-cast pulley which has been accurately and carefully machined. This runs on a centre spindle with a gently radiused tip that's supported on a plastic pad at the bottom of a deep phosphor bronze bush in a substantial die-cast housing. Upon this the 12in platter rests, which is another large casting that has been dynamically balanced with lead weights fitted at selected positions around its perimeter.
Rare Treat
For optimal damping the platter features a bonded mat and has strobe rings cast into its underside to aid in fine tuning the speed, which is 33rpm only. An orange neon lamp illuminates the strobe, and the position of this can be changed for 50Hz and 60Hz markets. The strobe is viewed via an intricate set of lenses and mirrors, the window being just to the left of the stylus tip when the tonearm is at rest.
The arm too shows many examples of considered design. The downforce is applied dynamically using a spring-loaded roller on the pivot, the static setting being made by a counterweight which is decoupled by a soft plastic insert. The counterweight screws in and out for fine adjustments, or it can be telescoped in and out for larger changes, such as those that may be needed if fitting a heavier cartridge.